Today is the day we finally start stitching the boat together!
But first, what a morning! Early wake up with the kids, prep and deliver said children to respective day care / schools, pick up medication, pick up Chris, drop off new bed to sister and then, finally, drive down the coast to the shed and the awaiting boat.

It was again a gorgeous blue sky with a light easterly wind blowing offshore. Our container seemed to have withstood the recent wild weather so we got to work laying out the hull and first layer ready for stitching. The pieces, which we’d already glued together into the respective planks, were laid out across three saw horses. The 17 feet of length becomes very apparent now in our 20 foot container so we needed to ensure that we can still access the prep table and shelving at the back but keep the entire boat inside the container.

We start by cutting 40cm lengths of copper wire with the always trusty Sammy the Snipper, noting that the old smart phone had to be used to measure and mark out the 40cms on the workbench #forgottheruler.
The copper wire is then inserted into pre-cut holes along the hull and side planks, joining the two together.
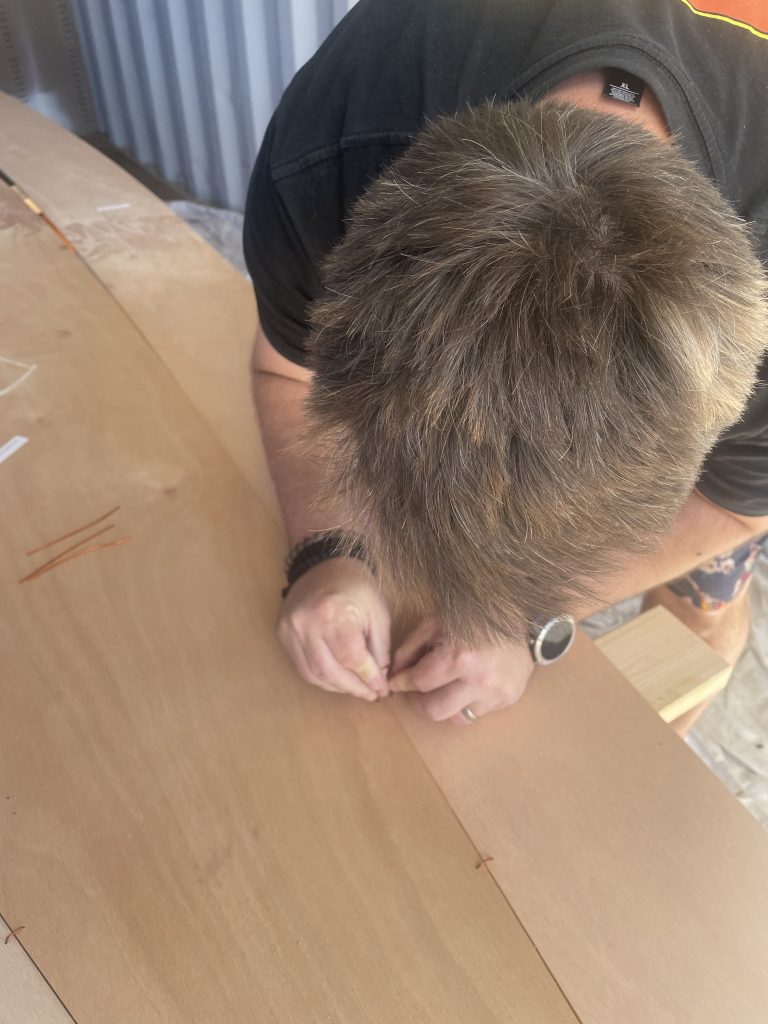
The wire is loosely twisted together so that the planks can be moved a little, which becomes important as you add the bulkheads into the shell. The bulkheads are like the ribs in appearance. They form the shape of the boat and provide a frame upon which the remaining planks are stitched against. Each bulkhead had two tabs at the base that fit, with encouragement, into two similar sized holes on the hull. along the edges there were holes through which copper was threaded through and into the hull and side planks. Pro tip – insert the copper wires into the bulkhead before placing it onto the hull. You’ll thank me later.
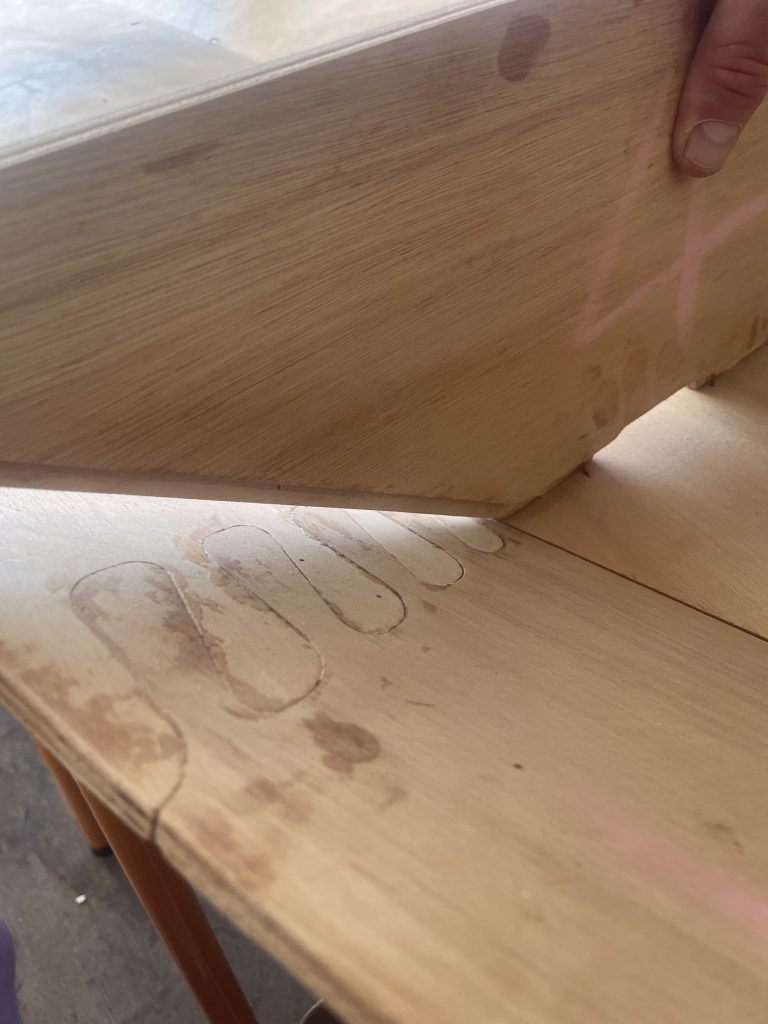
A recurring problem we’ve encounter with a bunch of boat pieces machined by someone over 4,000 kms away, despite their undeniable enthusiasm and expertise, is that not everything is drilled or filed. It’s not like a flat packed bedside table – you still have to roll up the sleeves and prepare to get sawdust on you… well Chris does.
Every so often we came across a hole that had been glued over or not drilled. Given our history of not having the right tools for the job, you can guess the answer to Chris’ innocent “where’s the drill?”. Fortunately we discovered Ned the Nail and his mate Handy Hammer. Whammo – problem solved.
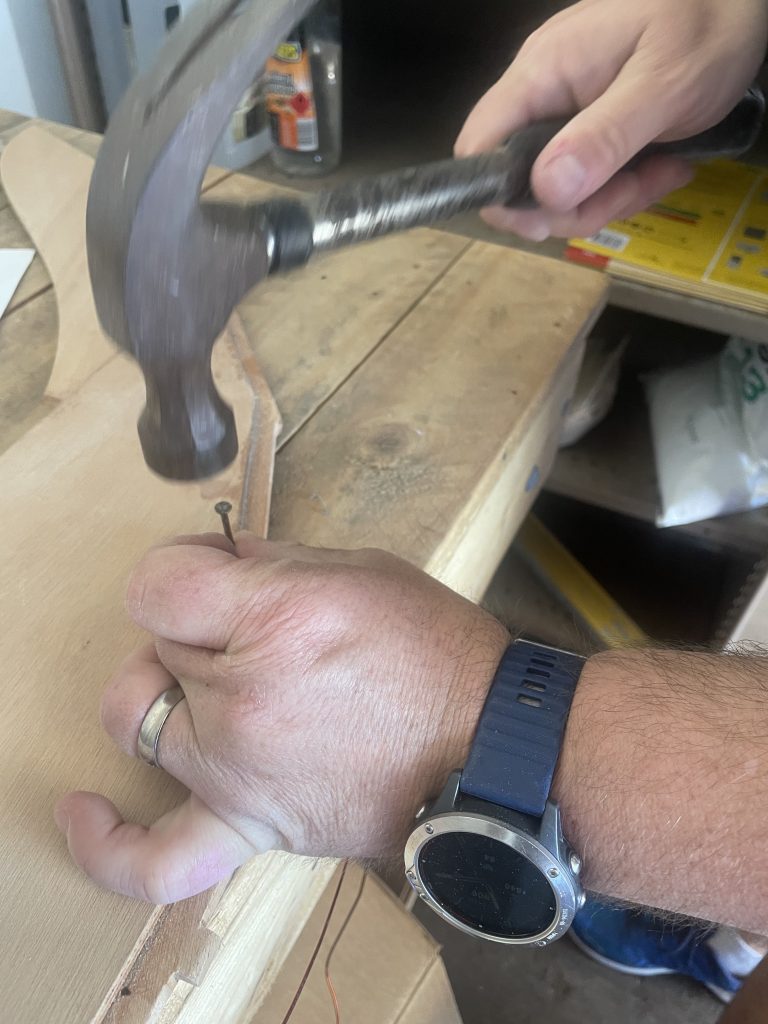
Eventually, with the finesse of two mallards, we had the hull, bulkheads and first plank layer stitched together. What a great feeling to see the boat start coming together! Next time we’ll be stitching the next two side planks on.
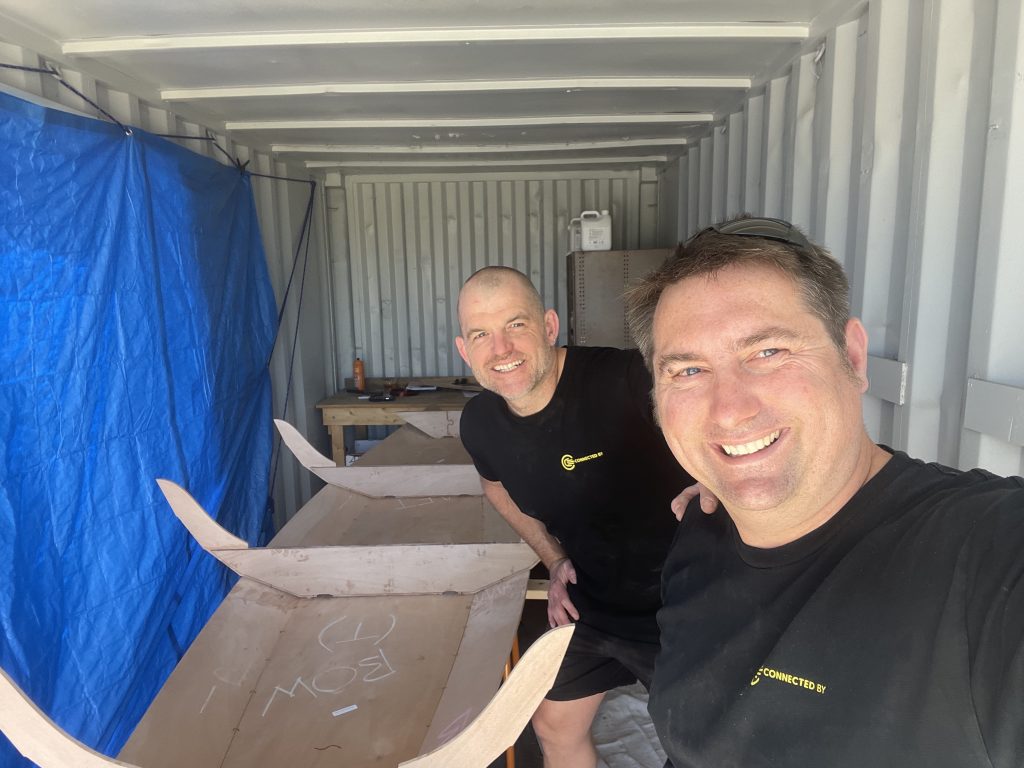