The man who never makes enny blunders seldum makes enny good hits
Josh Billings, 1874
Within the brilliant is the mundane, as such, for your sanity and the readability of this blog, I’m going to summarise four days of epoxy work into one sentence for you… [ahem!]…
Don’t epoxy when the temperature is above 30*C (86*F).
Simple advice really. Unfortunately all the guidance we have is from the northern hemisphere or Tasmania where it is a touch cooler. So my advice to aspiring wooden boat-building Aussies is to time your epoxy labour so that its in winter. If you don’t, then use small amounts and be quick about it. You’d have thought we had learnt from our last foray into epoxy (see Day 3) but no. Like a pair of pelicans, we leant into this mistake with ham fists and addled brains.
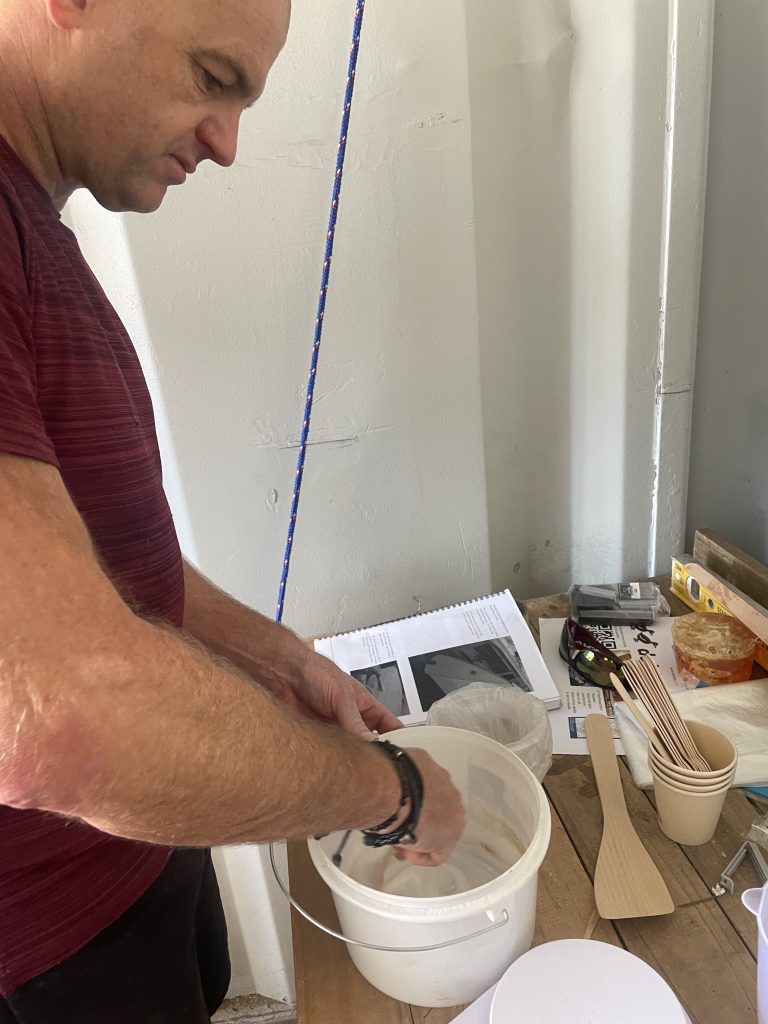
Once again, full of optimism and false hope, we set about mixing the epoxy with cell-o-fill (that fine fibreglass dust) to the consistency of mustard or another condiment – just not sauce! – and set about filling the gaps between each lap. Each pass we planned to carefully avoid the copper stitches to prevent them from being “forever entombed”.
I used a small plastic sandwich bag as recommended by our false CLC gods to squeeze ribbons of thickened epoxy into the gaps and Chris followed behind with a flat piece of wood and cloth to smooth out the epoxy fillets.
Insert real time chemistry to smash our confidence. The epoxy cooked off so quickly in the bag that I flung the burning mess outside onto the concrete with a string of curses. Sweat beaded off Chris’ forehead while he attempted the impossible to smooth the rapidly hardening epoxy. It was no good. As the baggy smouldered on the concrete the fillets bubbled. I was physically damaged (figuratively speaking dear readers) and Chris was emotionally damaged. Our day was done. Slam that door shut and deal with it another day.
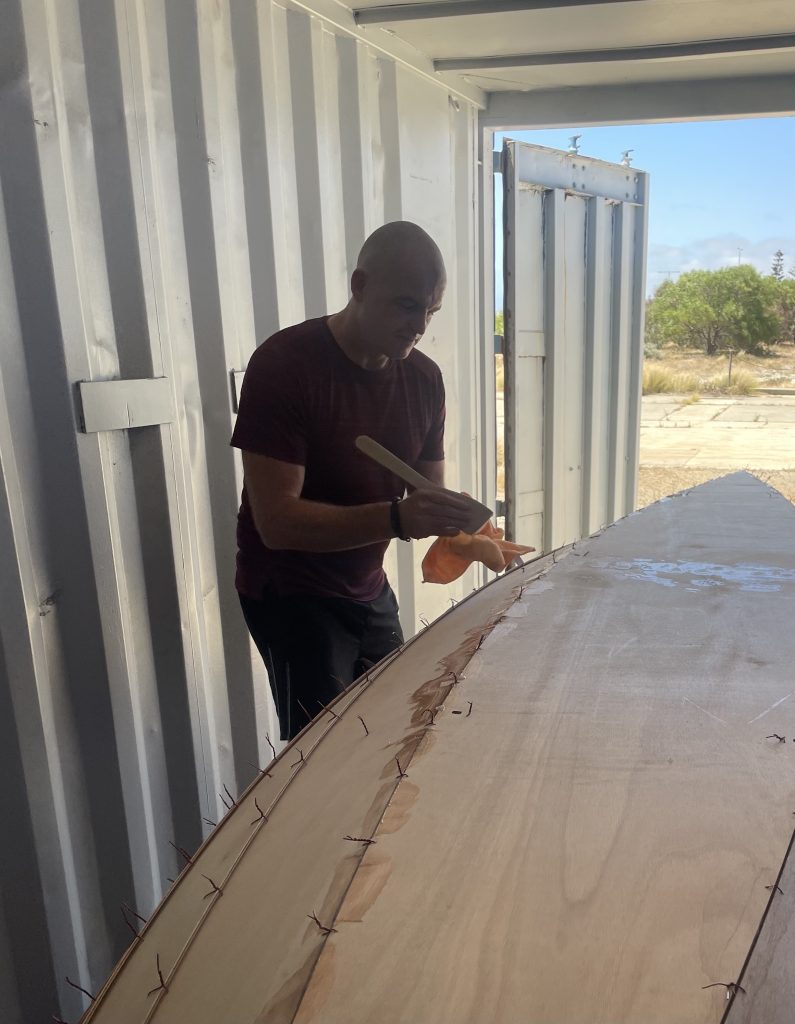
So scarred were we that it was another two weeks before we returned. Admittedly it was school holidays so I took a couple of our kids camping down at Dwelingup and then to Preston Beach. It was a good break and allowed Chris and I to rethink our strategy.
We returned on another superb summer day to crack the container and have a look at the damage. Hearts in our mouths we drew the doors ajar…

Mother of all that is wrong in the world – what the bejesus was this. This was a right proper bollocks up. The epoxy had cooked and made a mess of the fillets, a mess oft seen in kindergarten baking. Lumpy and irregular, it burned our eyes and pride just looking at it.
Decision time. Grind back the epoxy to start again or just continue on..
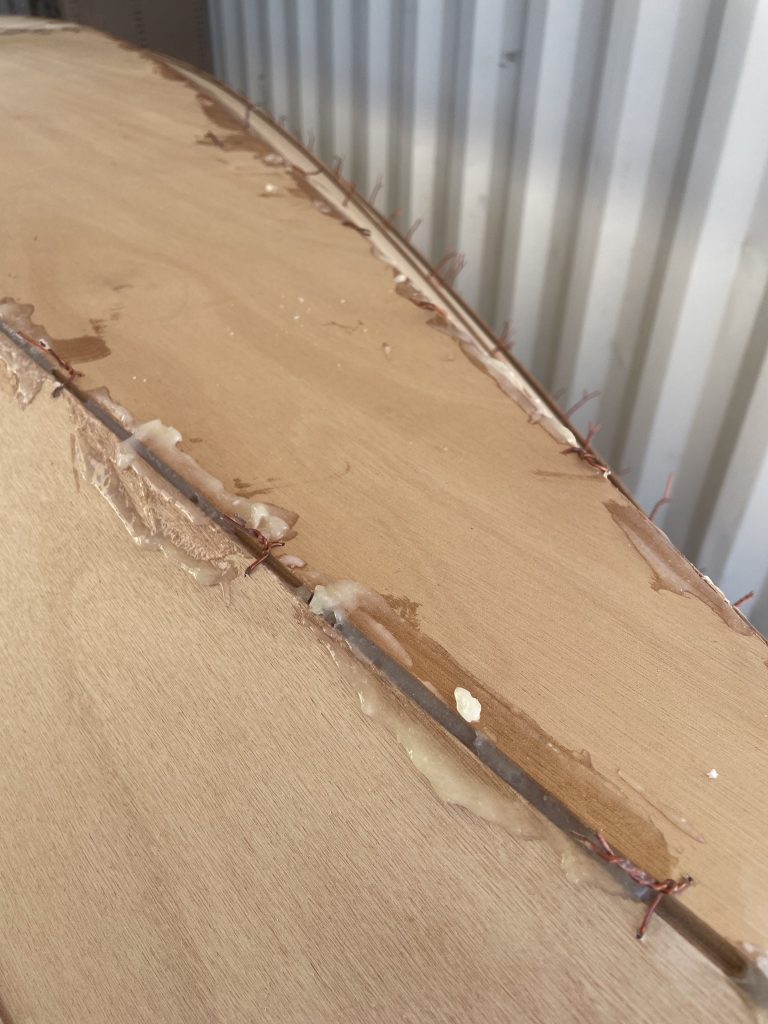
Obviously we continued on. I wasn’t going to waste a beautiful day revisiting a dog’s breakfast. it was time to push that mistake deep down and pretend it didn’t happen.
This time I mixed only 100g of epoxy with 4-5 scoops of cell-o-fill and 20g of hardener. This gave us consistency and time to smooth the fillets. How far could one do with 100g of epoxy? As it turned out, about 2/3 the length of the boat.
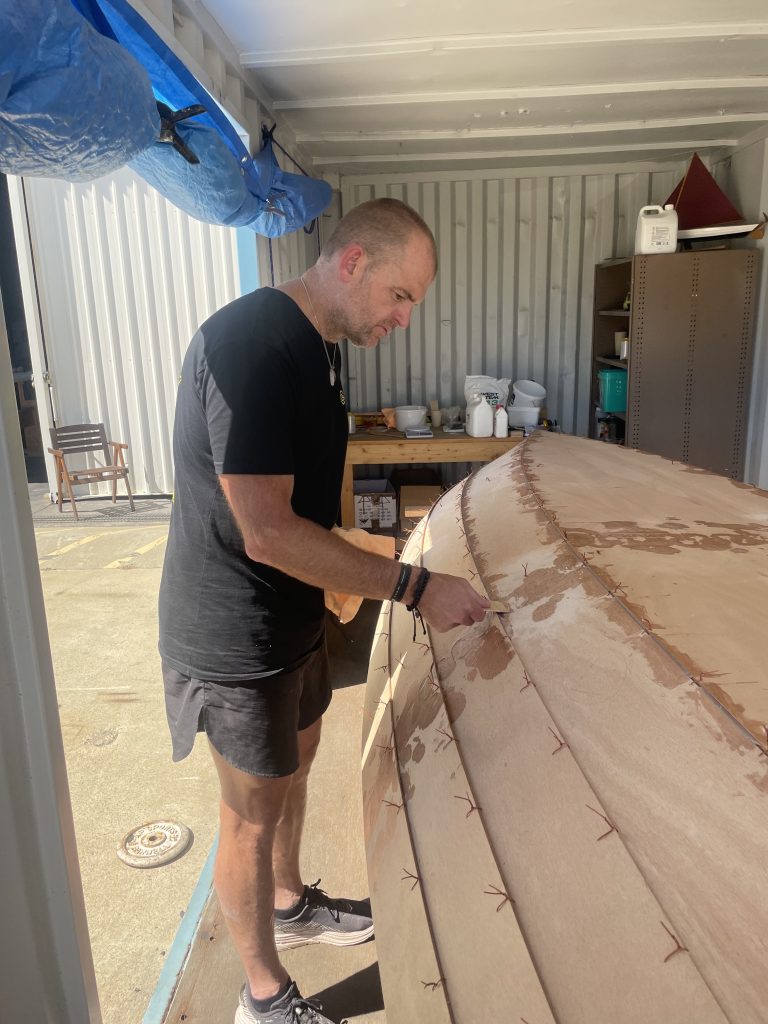
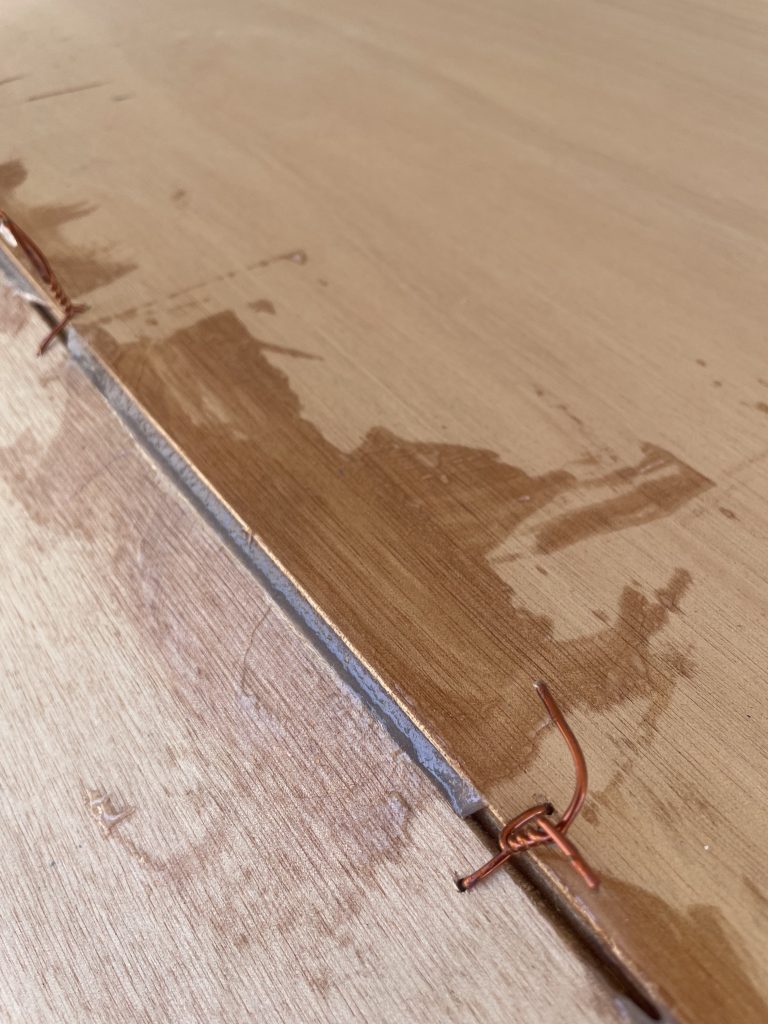
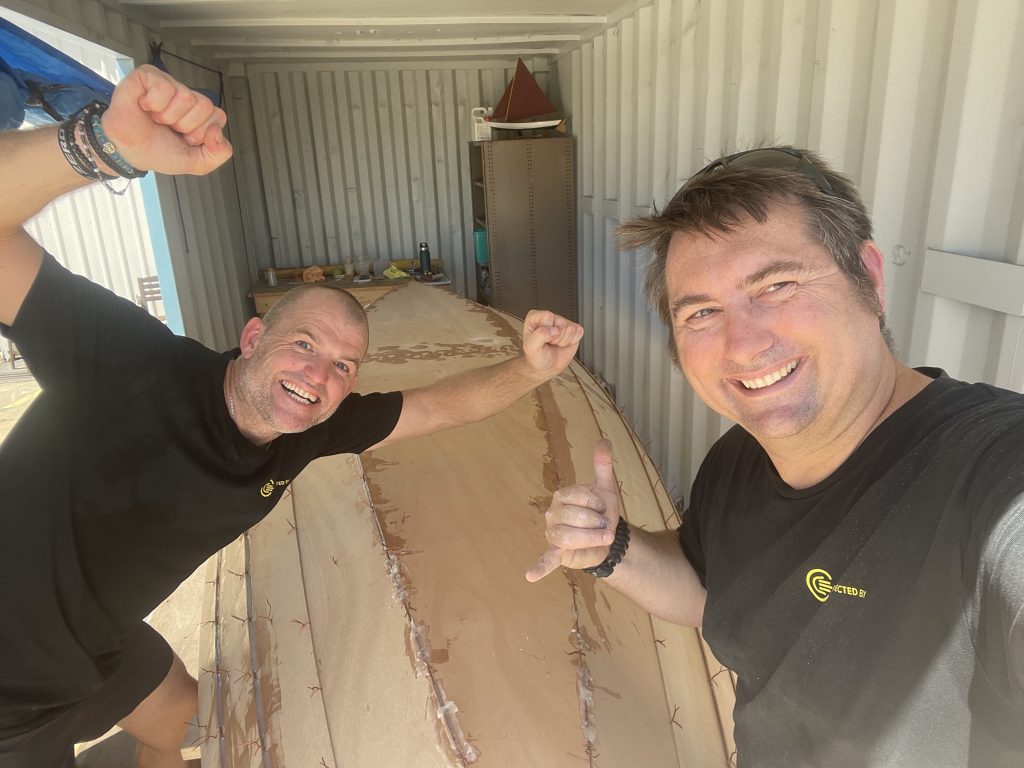
What a day. Our consistency, volume and timing was spot on. Team dublduck were back! I struggle to describe how awesome it felt getting this “simple” job right.
Unfortunately because we were dealing super small volumes and had a limited supply of ice-cream tubs – which are perfect to flex out the old epoxy and re-use – so we couldn’t complete the epoxy in that day. In fact it was another two more days of work (representing a month of real time) before we were able to complete the outside epoxy. We were thrilled. Job well done. And the debacle on the bow? We left that alone for future Reece and Chris to deal with.
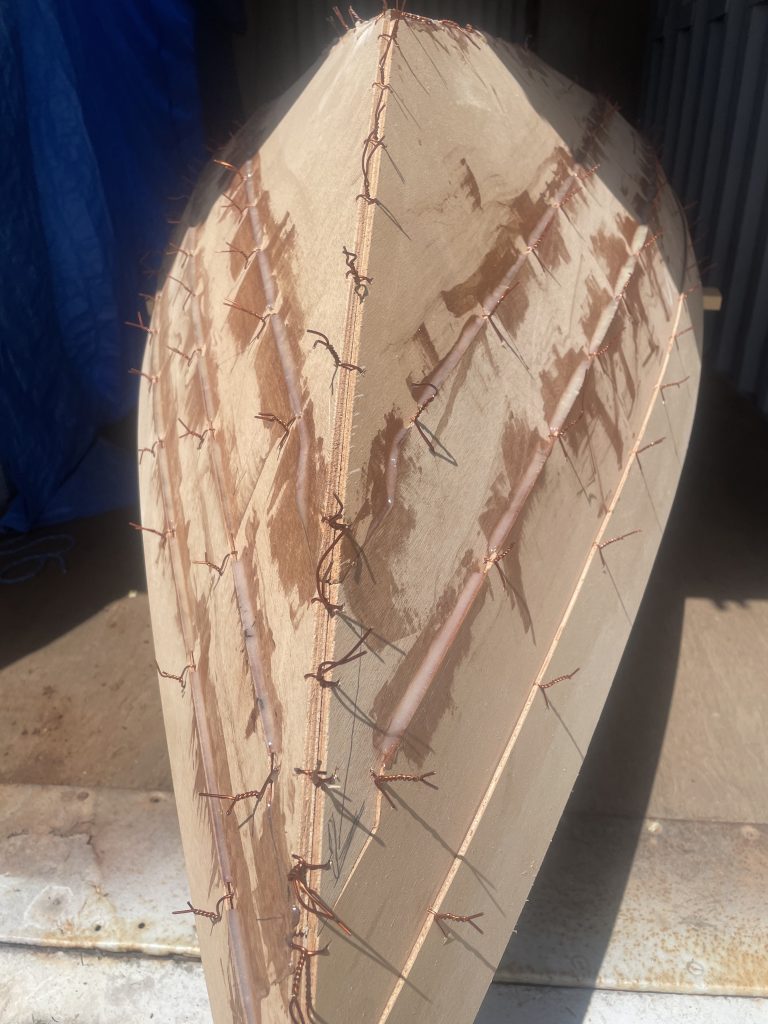
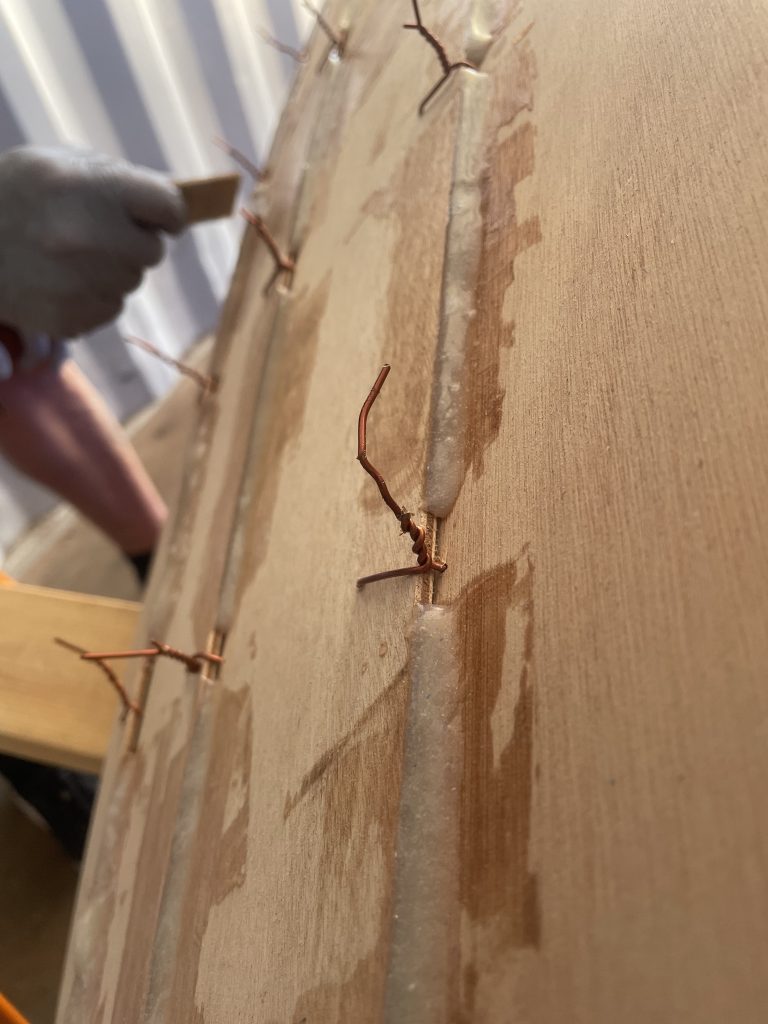
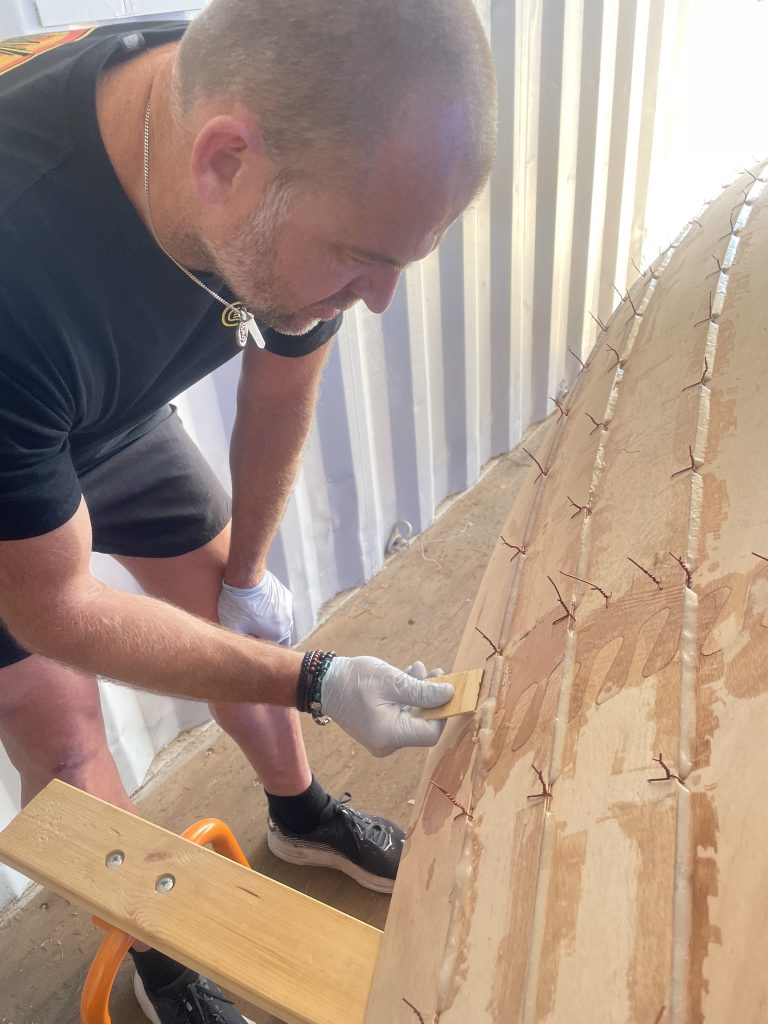
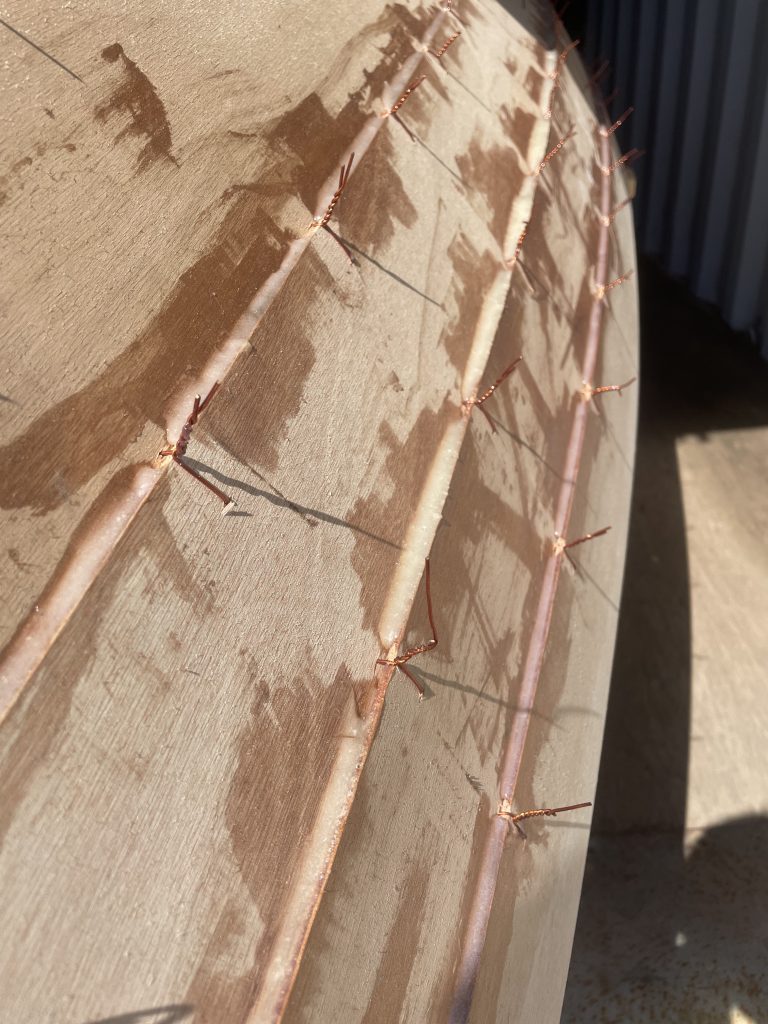
Join us next time when we flip the boat and think about fibreglassing the interior.